Unveiling the Enigmatic World of Sheet Metalists: An In-Depth Guide
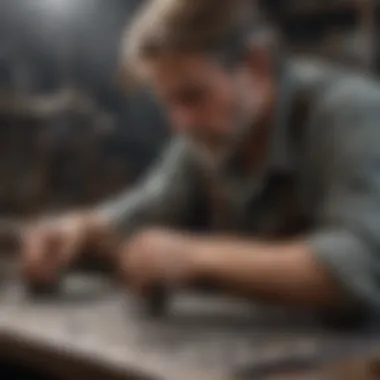
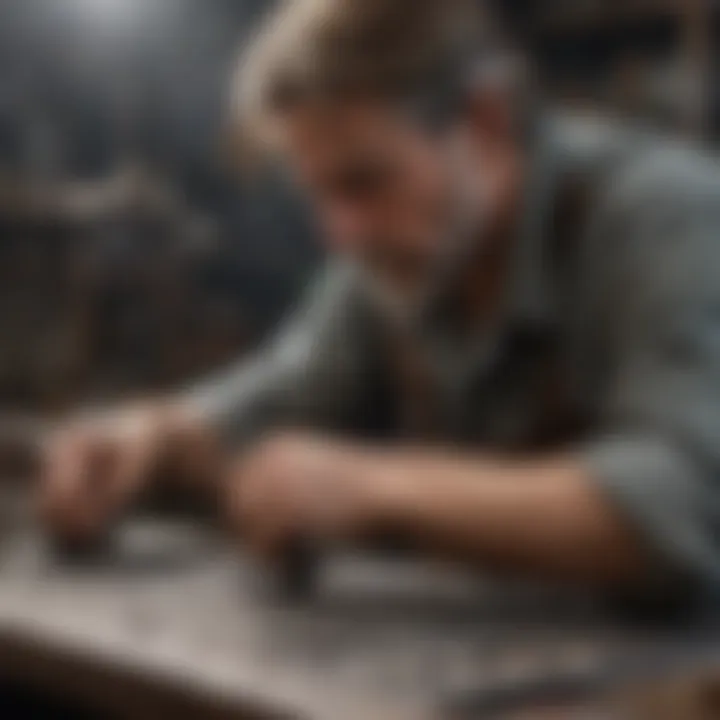
Market Insights
- Current Trends and Developments:
In the dynamic realm of sheet metal fabrication, staying abreast of current trends is paramount. With the advent of advanced technologies such as laser cutting and CNC machining, traditional methods are evolving to meet the demands of precision and efficiency. Techniques like hydroforming and deep drawing are gaining popularity, showcasing the industry's adaptability.
- Market Analysis and Predictions:
Conducting a thorough market analysis unveils the landscape of opportunities and challenges within the sheet metal sector. Insights into consumer preferences, production costs, and emerging design trends can guide strategic decision-making. Predictions based on market dynamics and economic indicators enable proactive measures to capitalize on growth potentials.
- Sector-Specific Insights:
Delving into sector-specific insights provides a focused understanding of niche markets within sheet metal fabrication. Whether catering to automotive, aerospace, or architectural industries, adapting tooling and techniques to align with sector requirements is essential for sustained relevance and competitiveness.
Economy Insights
- Economic Indicators and Metrics:
Economic indicators play a pivotal role in gauging the health of the sheet metal industry. Metrics such as GDP growth, inflation rates, and industrial output influence the demand for fabricated metal products. Monitoring these indicators offers valuable foresight into market trends and potential shifts.
- Government Policies and Impacts:
Government policies wield significant influence on the sheet metal landscape, spanning regulations on environmental compliance, trade agreements, and industry tariffs. Understanding policy impacts is crucial for devising sustainable business strategies and navigating compliance requirements effectively.
- Global Economic News:
Amidst the backdrop of a global economy, staying attuned to international developments is imperative for sheet metalists. Fluctuations in currency exchange rates, geopolitical tensions, and trade relations can reverberate through the metal fabrication sector, necessitating agile responses to safeguard business interests.
Investment Strategies
- Portfolio Diversification:
Diversification is key to mitigating risks and enhancing investment returns in the sheet metal domain. Allocating assets across varied segments such as custom fabrication, mass production, and specialty applications can shield portfolios from market volatilities and sector-specific downturns.
- Risk Management Techniques:
Effective risk management hinges on adeptly assessing and mitigating potential threats in sheet metal investments. Tools like financial derivatives, hedging strategies, and scenario planning help safeguard against unforeseen market fluctuations, ensuring a resilient investment portfolio.
- Investment Evaluation Criteria:
Sound investment decisions are underpinned by robust evaluation criteria tailored to the sheet metal industry. Factors like ROI projections, market feasibility studies, and competitor analysis offer a systematic framework for evaluating investment opportunities and optimizing resource utilization.
Personal Finance Tips
- Budgeting and Saving Strategies:
Thriving in the world of sheet metal fabrication requires sound financial management practices. Implementing budgeting and saving strategies empowers individuals to streamline expenses, build financial reserves, and weather cyclical fluctuations in the metalworking sector.
- Retirement Planning Guidance:
Long-term financial security is a cornerstone of personal finance for sheet metalists. Crafting a well-defined retirement plan encompassing pension schemes, investment accounts, and succession strategies ensures a stable financial future post-career, underscoring the importance of prudent financial foresight.
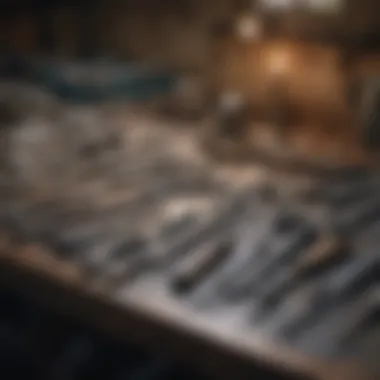
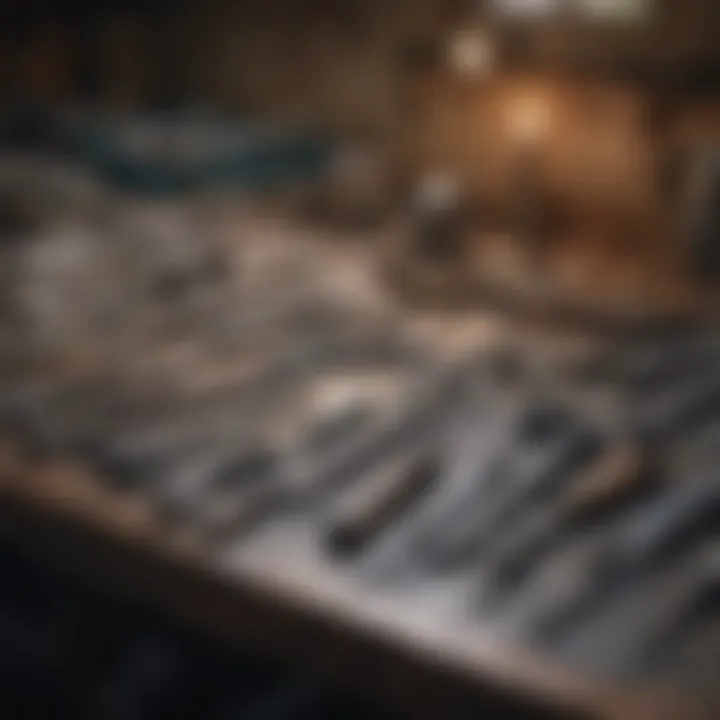
- Debt Management Tips:
Navigating debts judiciously is imperative for maintaining financial equilibrium in the sheet metal industry. Adopting debt management techniques such as debt consolidation, repayment prioritization, and interest negotiation facilitates prudent financial decision-making, empowering individuals to manage liabilities effectively.
Case Studies and Success Stories
- Real-Life Practical Examples:
Illustrative case studies shed light on real-world applications of sheet metal fabrication, showcasing innovative solutions, technical challenges overcome, and operational excellence achieved. Drawing insights from practical examples elucidates best practices and inspires creative problem-solving within the sheet metal domain.
- Successful Investment Stories:
Success stories of astute investments in sheet metal ventures provide a roadmap for aspiring investors seeking lucrative opportunities. Examining the trajectories of successful investments unveils valuable lessons, strategic insights, and risk management approaches essential for attaining investment success in the metal fabrication realm.
- Personal Finance Transformation Journeys:
Personal finance transformation narratives chronicle the evolution of financial destinies within the sheet metal industry. From financial setbacks to triumphs, these stories underscore the significance of resilience, perseverance, and strategic financial planning in shaping prosperous personal finance trajectories within the metalworking profession.
Prolusion
Sheet metalists are artisans who manipulate thin sheets of metal through a variety of techniques, creating a wide array of products. Their skills and expertise are crucial in industries like manufacturing, construction, and automotive. Understanding sheet metalists and their craftsmanship allows us to appreciate the intricate processes involved.
Defining Sheet Metalists
Skills and Expertise
Sheet metalists possess exemplary skills in measuring, cutting, bending, and shaping metal sheets accurately. Their meticulous attention to detail ensures high precision in their work, resulting in finely crafted products. The ability to interpret technical drawings and work with different metals sets them apart, making their expertise highly sought after.
Materials Used
The materials used by sheet metalists vary from stainless steel and aluminum to copper and brass. Each material has distinct properties and advantages, influencing the final product's performance and appearance. Understanding the characteristics of various metals is vital for sheet metalists to select the appropriate material for each project.
History and Evolution
The history of sheet metalistry dates back centuries, with ancient civilizations like the Egyptians and Greeks employing metal in various forms. Over time, advancements in technology have revolutionized sheet metal techniques, leading to increased efficiency and precision in manufacturing processes. Studying the evolution of sheet metalistry provides valuable insights into its significance today.
Significance in Modern Industry
Role in Manufacturing
Within modern industry, sheet metalists play a pivotal role in fabricating essential components for machinery, vehicles, and infrastructure. Their ability to convert raw metal sheets into functional products streamlines manufacturing processes and ensures product quality. The precision and expertise of sheet metalists contribute significantly to the efficiency of production lines.
Innovations and Technologies
Advancements in technologies such as CNC machining and 3D printing have revolutionized sheet metalistry, enabling intricate designs and faster production cycles. Sheet metalists leverage these innovations to expand their capabilities and offer bespoke solutions to clients. Embracing technology is paramount for sheet metalists to stay competitive in the ever-evolving industrial landscape.
Impact on Various Sectors
The impact of sheet metalists transcends industries, with their creations contributing to sectors like aviation, architecture, and renewable energy. Innovations in sheet metal techniques have opened up new possibilities for product design and functionality. The adaptability of sheet metalists in catering to diverse sectors underscores their significance in driving innovation and development.
Understanding Sheet Metal Techniques
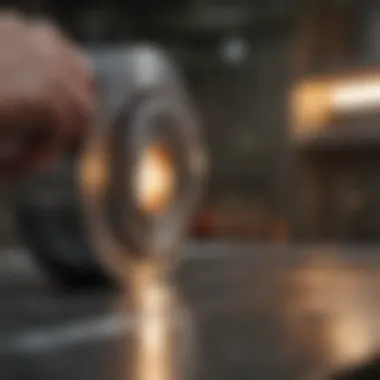
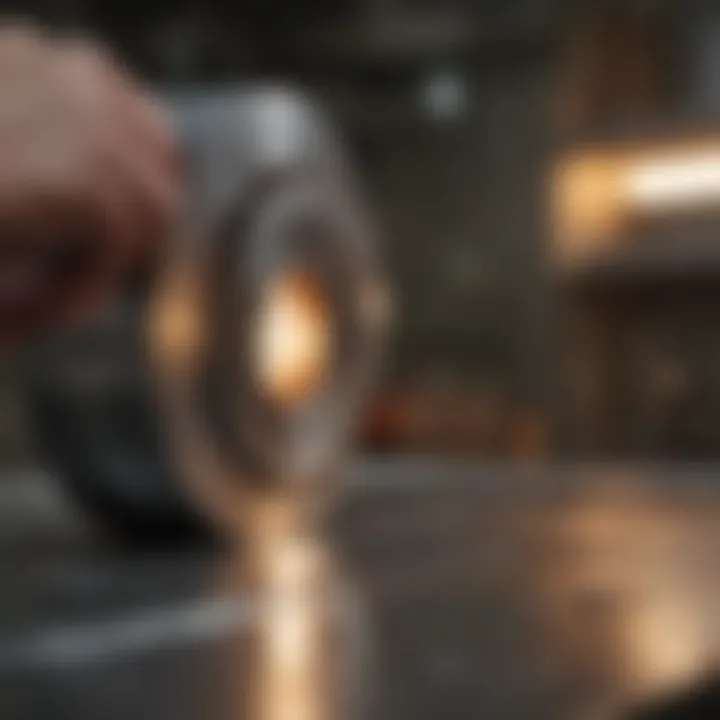
Exploring the world of sheet metalists involves delving deep into the intricate techniques and methodologies that define this specialized craft. In this section, we will explore the significance of understanding sheet metal techniques, shedding light on the key elements that contribute to the mastery of this art form. From cutting and shearing to forming and bending, each aspect plays a crucial role in shaping the final outcome of sheet metal projects.
Cutting and Shearing
Types of Cutting
When we discuss the types of cutting in sheet metal work, we are referring to the diverse range of methods used to shape and size metal sheets according to project requirements. From laser cutting to plasma cutting, each technique brings its unique advantages and intricacies to the table. Laser cutting, for instance, offers unparalleled precision and control, making it a popular choice in the industry. However, plasma cutting excels in its ability to swiftly maneuver through thicker sheets, showcasing its versatility.
In the realm of sheet metalistry, the choice of cutting method is predominantly dictated by the project's specifications and desired outcome. Understanding the nuances of each cutting technique allows metalists to harness the full potential of their craft, ensuring accuracy and efficiency in their work.
Shearing Processes
Shearing processes in sheet metal work involve the use of shear blades to cut through metal sheets with exceptional precision. This method is particularly favored for its ability to produce clean, straight cuts, essential in achieving seamless fabrication. While shearing may seem straightforward, mastering this process requires a keen eye for detail and a steady hand.
Shearing processes contribute significantly to the overall quality of sheet metal projects by ensuring seamless edges and precise measurements. However, challenges such as material distortion and blade wear must be carefully managed to maintain optimal performance.
Precision Cutting Tools
Precision cutting tools are the backbone of every sheet metalist's toolkit, offering unparalleled accuracy and efficiency in shaping metal sheets. From rotary cutters to guillotine shears, these tools empower metalists to transform raw materials into intricate designs with utmost precision.
The integration of precision cutting tools not only streamlines the fabrication process but also ensures uniformity and consistency in the final product. However, it is essential to consider factors such as blade sharpness and maintenance to uphold the longevity and effectiveness of these cutting instruments.
Tools of the Trade
In the realm of sheet metalistry, the tools employed play a pivotal role in shaping the craft into a precise and efficient practice. The significance of tools in this domain cannot be overstated, as each tool serves a specific function aimed at ensuring accuracy and quality in the final products. From metal cutting tools to welding devices, the arsenal of equipment available to sheet metalists is diverse and tailored to meet the demanding requirements of the industry.
Essential Equipment
Metal Cutting Tools
When delving into the domain of sheet metal cutting, one cannot overlook the importance of high-quality metal cutting tools. These tools are engineered to carve through metal sheets with precision, offering a clean and accurate cut essential for crafting intricate designs. The key characteristic of metal cutting tools lies in their durability and sharpness, allowing for seamless operation and minimal material wastage. Furthermore, their versatility makes them a popular choice among sheet metalists, enabling them to work with various metals effectively. Despite their advantages, metal cutting tools may pose challenges in terms of maintenance due to the wear and tear resulting from consistent use.
Forming Machinery
The utilization of forming machinery is integral to the sheet metal production process, facilitating the shaping of metals into desired forms. This equipment's key characteristic lies in its ability to bend and mold metal sheets accurately, ensuring compliance with intricate design specifications. Forming machinery is a preferred choice for many sheet metalists due to its efficiency in large-scale production and ability to produce complex shapes with consistency. However, one should note that the initial investment and maintenance costs associated with forming machinery can be substantial.
Welding Devices
Welding devices hold a prominent position in the toolkit of sheet metalists, enabling them to join metal components securely. The key characteristic of welding devices is their capacity to create strong and durable bonds between metal pieces, vital for constructing robust structures. This equipment's popularity stems from its reliability and effectiveness in fusing diverse metals, expanding the creative possibilities for sheet metalists. Despite their advantages, welding devices may present challenges in terms of ensuring uniform weld quality and protecting against potential hazards such as heat-related injuries.
Advanced Technology
CNC Machining
In the realm of sheet metal fabrication, CNC machining stands out as a cutting-edge technology revolutionizing production processes. The key characteristic of CNC machining is its precision and efficiency in executing intricate designs with minimal margin for error. This technology is a beneficial choice for sheet metalists looking to enhance productivity and accuracy in their operations. However, the primary disadvantage of CNC machining lies in the high initial investment required for the equipment and training, which may pose a barrier for smaller enterprises.
3D Printing in Sheet Metal
The integration of 3D printing in sheet metal work introduces a new dimension of flexibility and innovation to the craft. The key characteristic of 3D printing lies in its ability to create complex metal structures layer by layer, offering a level of detail and customization previously unattainable. Sheet metalists are drawn to this technology for its rapid prototyping capabilities and cost-effective production methods. Nonetheless, challenges such as material limitations and slower production speeds may impact its widespread adoption in certain applications.
Diagnostics and Inspection
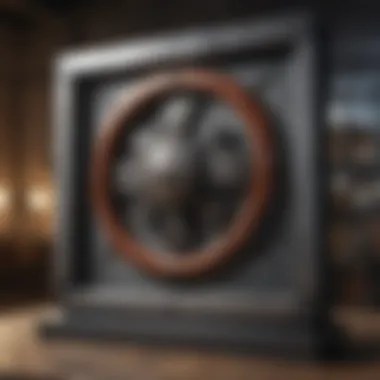
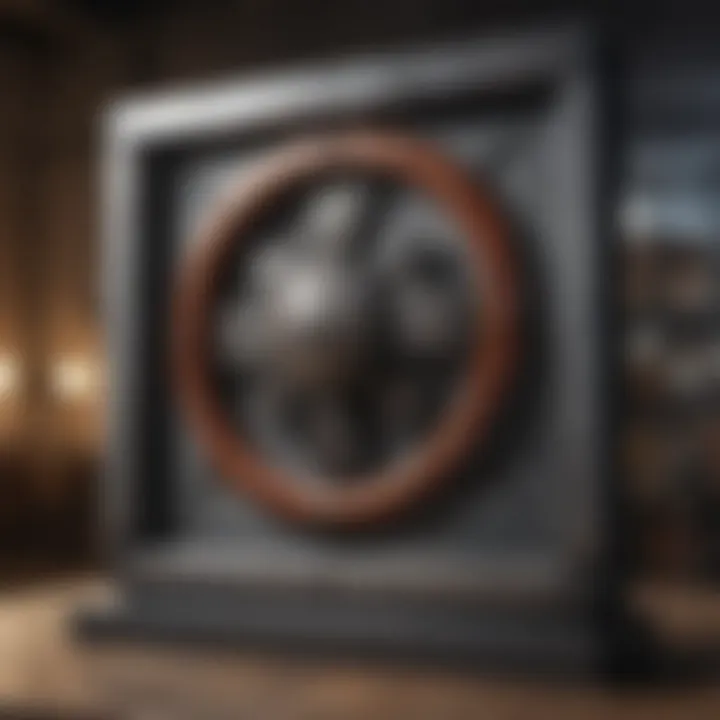
Diagnostics and inspection technologies play a critical role in ensuring quality control and precision in sheet metal production. The key characteristic of these tools is their ability to detect flaws and deviations in metal components, safeguarding against defects and ensuring compliance with stringent industry standards. Sheet metalists benefit from the thorough assessments offered by diagnostics and inspection devices, allowing them to deliver high-quality products consistently. Nevertheless, the challenge lies in the time and resources required to conduct comprehensive inspections, which may impact production timelines and costs.
Tools are the extension of a craftsman's expertise, amplifying their capabilities to transform raw materials into intricate creations. Understanding the nuances of each tool and technology is essential in mastering the art of sheet metalistry.
Mastering Sheet Metal Craftsmanship
Craftsmanship within the realm of sheet metal holds a paramount significance in the multifaceted world of manufacturing. Every bend, cut, and join exemplifies a meticulous artistry that not only demands precision but also ingenuity, illustrating a blend of skill and creativity. Mastering Sheet Metal Craftsmanship encapsulates the essence of transforming raw metal sheets into intricate structures through a symphony of techniques and expertise.
Training and Education
Apprenticeships:
Apprenticeships, as a cornerstone of artisanal progression, offer aspiring metalists a gateway to immerse themselves in the rigors of sheet metal craftsmanship. Whether honing skills in shaping metal or fine-tuning welding techniques, apprenticeships provide a hands-on learning experience that cultivates not just technical proficiency but also a deep-rooted appreciation for the craft.
Certification Programs:
Certification programs serve as a testament to one's mastery of sheet metal techniques, validating proficiency and enhancing credibility within the industry. Upholding standards of excellence, these programs equip metalists with the knowledge and expertise required to navigate the complexities of modern metalwork, underscoring the commitment to continuous growth and skill refinement.
Continuing Education:
In a dynamic landscape of technological advancements and evolving practices, continuing education emerges as a pivotal avenue for metalists to stay abreast of industry trends and innovations. By engaging in ongoing learning opportunities, professionals can adapt to changing paradigms, expand their expertise, and explore new frontiers in sheet metal craftsmanship.
Industry Insights
Career Opportunities:
Navigating the realm of sheet metal opens doors to a spectrum of career opportunities, ranging from metal fabrication to industrial design. The versatility of sheet metal craftsmanship empowers individuals to diversify their skill set and explore niche fields, fostering a dynamic and fulfilling career path shaped by innovation and craftsmanship.
Market Trends:
Keeping a pulse on market trends is essential for sheet metalists aiming to align their practices with industry demands and consumer preferences. From the rise of sustainable metalwork solutions to the integration of cutting-edge technologies, staying attuned to market trends enables professionals to innovate, adapt, and thrive in a competitive landscape.
Challenges and Innovations:
Embracing challenges fuels innovation within the sheet metal sector, prompting professionals to push boundaries and engineer solutions that transcend convention. Whether tackling material limitations or crafting novel fabrication techniques, addressing challenges head-on incites a culture of continuous improvement and fosters a spirit of innovation among metal craftsmen.
Future Trends in Sheet Metalistry
Around the corner, Future Trends in Sheet Metalistry beckons, offering a glimpse into the path the industry is set to tread. Within this section, we uncover the significance of embracing advancement in sheet metal craft. By delving into sophisticated techniques and technologies, we aim to equip readers with foresight into the trajectory of the sector.
Automation and Robotics
AI Integration
Artificial Intelligence Integration is not merely a buzzword but a pivotal cog in the wheel of progression for sheet metalistry. The intrinsic ability of AI to enhance precision and efficiency in metal fabrication processes can't be overstated. The amalgamation of AI with sheet metal works engenders a realm where accuracy meets speed seamlessly. This symbiosis between artificial intelligence and the meticulous artistry of sheet metal craftsmanship heralds a new era of unparalleled productivity in the domain. While the advantages are evident, the crucial aspect remains the cautious evaluation of AI's role to mitigate any potential downsides.
Robotic Fabrication
In the spotlight, Robotic Fabrication emerges as a catalyst reshaping the landscape of sheet metal industries. The essence of robotic arms tirelessly executing tasks once solely dependent on manual labor underscores the transformative power of automation. The streamlined workflows augmented by the reliability and consistency of robotic fabrication underscore its pivotal role in defining the future of sheet metal fabrication. While its merits are numerous, discerning the optimal balance between autonomy and human intervention is key to maximizing the benefits of robotic fabrication.
Industry 4. Impact
The advent of Industry 4.0 unravels a tapestry of possibilities within the realm of sheet metalistry. The convergence of cyber-physical systems with manufacturing unveils a paradigm shift encapsulating connectivity, automation, and data exchange. The profound impact of Industry 4.0 manifests in the form of improved operational efficiency, predictive maintenance, and accelerated innovation cycles. Embracing this digital evolution necessitates strategic integration to harness the full potential of the fourth industrial revolution in the sheet metal sector. As organizations traverse this transition, comprehending the nuances of data-driven decision-making becomes imperative.
Sustainability Practices
Within the realm of Sustainability Practices, the veracity of eco-conscious initiatives unfolds to redefine the ethical ethos of sheet metal craftsmanship. A conscientious shift towards sustainable practices not only aligns with environmental stewardship but also bolsters operational resilience within the industry. Through a holistic exploration of green solutions, recycling methodologies, and energy-efficient alternatives, the narrative converges on the imperative of balancing progress with environmental preservation. Navigating the terrain of sustainability in sheet metalistry mandates a nuanced understanding of implementing green strategies without compromising on operational efficacy and cost-efficiency.
- Green Initiatives: Within the purview of Green Initiatives, the emphasis on minimizing carbon footprints and promoting ecological balance casts a spotlight on the ecological side of sheet metal industries. By adopting green practices, organizations demonstrate a commitment to environmental sustainability while fostering a culture of responsibility towards future generations.
- Recycling in Metalwork: Proponents of Recycling in Metalwork champion a circular economy model, wherein discarded metal finds rebirth in innovative applications. The ethos of recycling extends beyond waste management to embody a philosophy of resource optimization, urging stakeholders to reevaluate traditional production paradigms in favor of sustainable metallurgical practices.
- Energy-Efficient Solutions: Embracing Energy-Efficient Solutions advocates for a harmonious blend of technological innovation and ecological sensitivity in sheet metalistry. By curating a spectrum of energy-saving measures, organizations not only curtail operational costs but also mitigate environmental impact. The integration of energy-efficient solutions in sheet metal operations catalyzes a transformative journey towards greener and sustainable industrial practices.